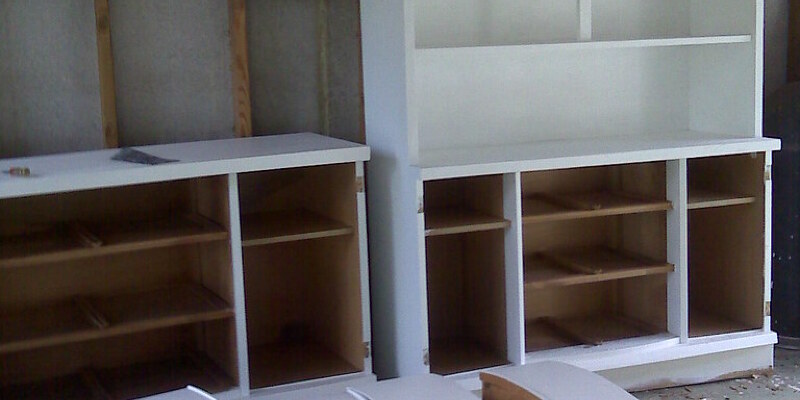
How to Use Resin to get a Decorative Countertop
Resin countertops, which might be epoxy, polyester or acrylic, have long been used in laboratory settings, as the non-porous nature of the material resists bacteria and stains. The parts of resins are fluid before they’re mixed. After mixing, they harden into a durable, strong material. Colored resins can produce a countertop which rivals materials such as polished soapstone, but you can gently tint the leaf for translucent color, or omit color to get a transparent appearance.
Prepare the Substrate
Resin needs a strong, flat substrate or foundation. Plywood, butcher block and medium-density fiberboard are acceptable. The substrate ought to be cut to fit the top of the cupboards with appropriate openings to the sink and other items such as a drop-in stovetop. Resin countertop substrates are attached to the cupboards from the underside with silicone adhesive or screws. Inserting screws down through the top of the substrate can cause a dip in the finished leaf at every screw. If the countertop demands more than one sheet of substrate, that is common in very long counters, seal the seams using two-part epoxy adhesive. You’ll need a temporary lip around the perimeter of the countertop and every opening to contain the fluid resin until it hardens. Strips of metal flashing tacked around the edges make a smooth lip, and its flexibility bends around curves.
Mix and Seal
Prior to pouring the bulk of the countertop, you should seal the substrate with a thin layer of leaf. Resin is made up of at least 2 components mixed together in a plastic container and used quickly. For clear resin that reveals the underlying material, you do not need a color additive in the sealer. This is common once the substrate has wood grain that you would like to show, such as with butcher block. A small quantity of resin goes on the substrate using a paint roller first. When you desire a solid or transparent color countertop, this is the opportunity to incorporate a leaf color additive. Bubbles may appear after rolling, but you may break them with a needle or toothpick. Some manufacturers recommend two applications of leaf for a sealer.
Artistic Touches
One of the benefits of a leaf countertop is the possibility for customization. You can seal just about any object beneath clear or lightly tinted resin and it will show through without being exposed to kitchen moisture. A countertop covered in jewels, such as pennies or nickels, adds a metallic beam without the typical care needed to maintain the metals. It is possible to seal in photographs, seashells, marbles, notes, tumbled sea glass or dried flowers and herbs. Fresh plant life is an exception, as the moisture content might interfere with the resin’s curing process. Photocopies and ink-jet printed items may run when leaf is pumped, so they are also a poor option. When the objects are lightweight, such as photographs, glue them to the sealed substrate using water-based adhesive and let the glue dry before proceeding.
Mix and Pour
Mixing resin to pour is just like mixing it to seal, except that you need more leaf. Even though you can pour the whole countertop at once, some manufacturers recommend pouring in layers, allowing each layer cure before adding another. Additional layers bonding seamlessly with all the underlying ones. Resin can set quickly. If the countertop is very large, you’ll need a helper to pour one place as you pour a second. Bubbles might form while pouring or soon after. If there aren’t any embedded objects, a propane torch passed gently across the leaf breaks the bubbles. If there are objects that the torch can damage, use a toothpick to break bubbles. After every layer sets, pour the next layer and then build until the depth that you prefer.
Cure and Complete
Curing time for leaf varies and may take up to a week. Anything put on the countertop before the resin cures can introduce permanent dents. Similarly, wait to install drop-in items such as the sink. You may safely get rid of the metal flashing lip before the leaf has completely cured as long as it feels company. If there are any drip marks on the edges, shave them away using the blade of a utility knife. Rough countertop edges are smoothed by sanding lightly with fine-grit sandpaper. Car wax, which has light synthetic ingredients, and a handheld, orbital polisher, such as a car-detailing polisher, buffs the sanded edges to a shine. You might also cover the edges with wood trim molding.